
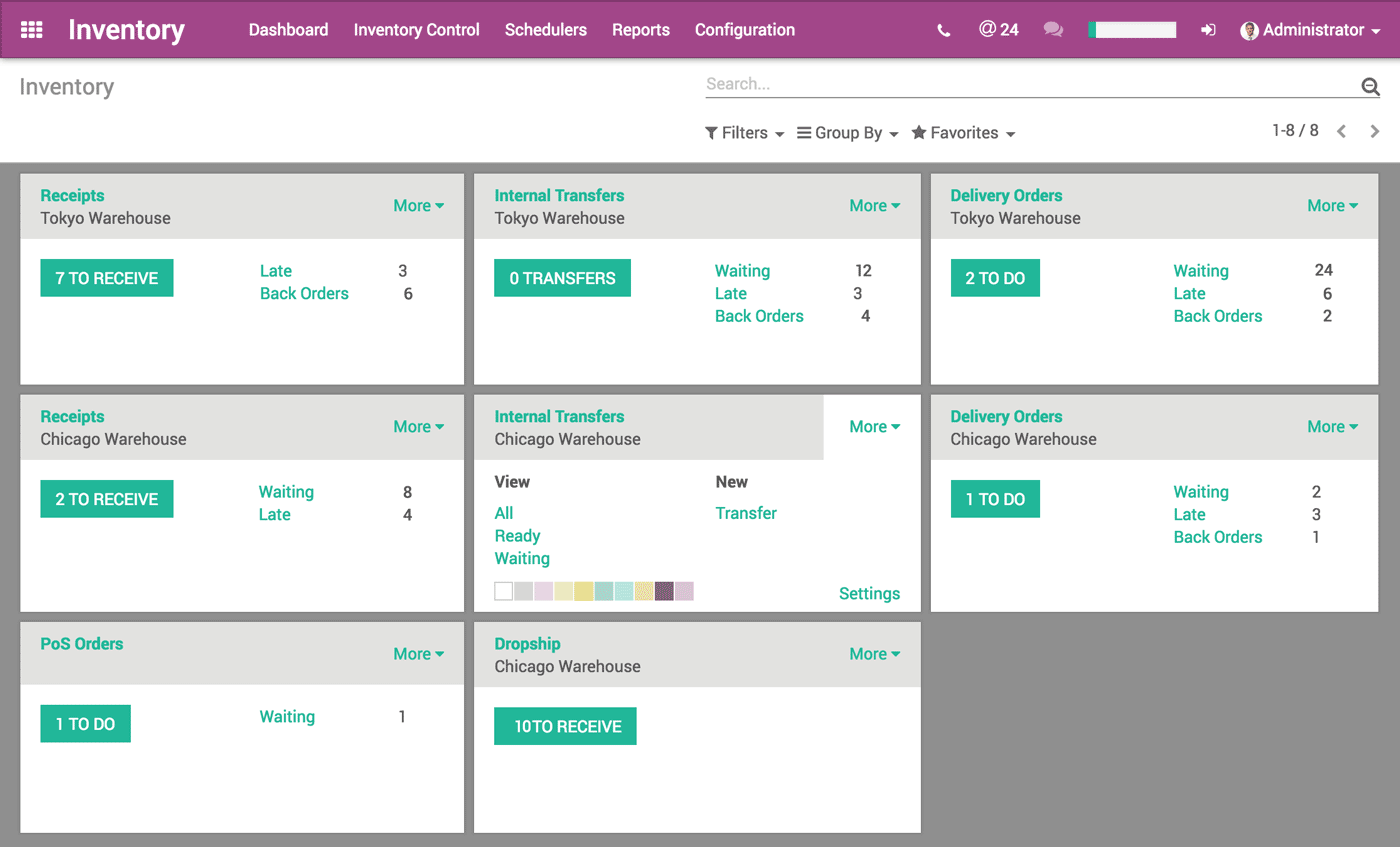
Accordingly, companies require a disciplined process to ensure that the level of inventory investment is in line with the expected level of customer demand. Slow-moving inventory incurs holding costs, risks, and adversely affects a company’s cash flow. Careful attention must be paid to the length of the cash conversion cycle-the time between purchasing raw materials (for a manufacturer) or merchandise (wholesaler or retailer) to the final sale of finished products and receipt of payments from customers.ĭuring that time, cash remains tied up, and companies must ensure their inventory is sold in a timely manner (called inventory turns) to return the cash to the business. Classified on the balance sheet as a current asset, inventory consumes company cash. Inventory management involves making trade-offs between revenue, cost, and risk. Inventory management: Financial implications Many procurement organizations take pricing discounts into consideration in their purchasing strategy and may buy more supply than required to obtain favorable price points. Demand-driven methods can include point-of-sale data from their retail customers. Local factors can include SKU-level demand, lead times, or seasonal patterns.

Distributors establish reorder points in a decentralized manner, allowing each distribution center to determine their inventory levels based on local factors or demand-driven methods. Manufacturers typically establish inventory controls, such as minimum and maximum stocking levels and reorder points, within their ERP systems. Stock-outs represent lost revenue and can adversely affect customer loyalty. The consequence of not having enough inventory are stock-outs, which can be detrimental to a business especially if customers have alternatives, such as ecommerce-based businesses where rapid fulfillment is expected. Safety stock represents a balance between service or fill rates (the percentage of customer orders that a company can ship immediately from stock) and the additional cost of ordering and holding more inventory. In this way, inventory functions as a protection against the unexpected, and as a buffer against production shutdowns. Manufacturers with expensive machine and people operations will sometimes carry excess inventory to avoid shutting down these operations due to a lack of inventory-which would cost the company more money.Īlmost all companies maintain safety stock inventory to protect against unexpected changes in supply and demand. Inventory costs the company money, but it may be necessary to hold more safety stock to maintain superior service levels to avoid stockouts and to maximize operational efficiency. Depending on their business model, companies use a number of different methods to manage inventory.
My stock inventory manager how to#
Deciding how to plan and manage inventory is a collaborative effort full of trade-offs, risks, and rewards. Inventory management is complex and varies depending on your industry, your function within the company, and the type of item being managed. Regardless of the type of business, companies must maintain tight control over inventory to conserve cash while ensuring they have enough stock to meet production schedules or forecasted customer demand and actual orders. Nonmanufacturing companies, such as wholesale distributors and retailers, stock finished goods for sale to final consumers.Īll companies must strike a balance between inventory levels and demand because inventory consumes a company’s cash and incurs carrying costs. Manufacturing companies purchase raw materials or components, store them until ready for production, and transform them into finished goods. Inventory can be broadly classified into three categories: raw materials/components, work in progress, and finished goods. Inventory strategy involves inventory management at the item level through policies, such as safety stock (described later), and to inventory controls through polices, such as ABC classification to prioritize replenishment rates, which take item level attributes, such as consumption value, lot sizes and order lead times, into account. In determining their, inventory strategy, companies make tradeoffs between minimizing the amount of cash tied up in inventory or holding more inventory to maximize customer service or production efficiency. Inventory management is generally performed at two levels: aggregate inventory management and stocking location and item-level inventory management. Inventory management is the process of orchestrating the flow of goods through a company in a continuous cycle of ordering, storing, producing, selling, and restocking goods.
